This website uses cookies so that we can provide you with the best user experience possible. Cookie information is stored in your browser and performs functions such as recognising you when you return to our website and helping our team to understand which sections of the website you find most interesting and useful.
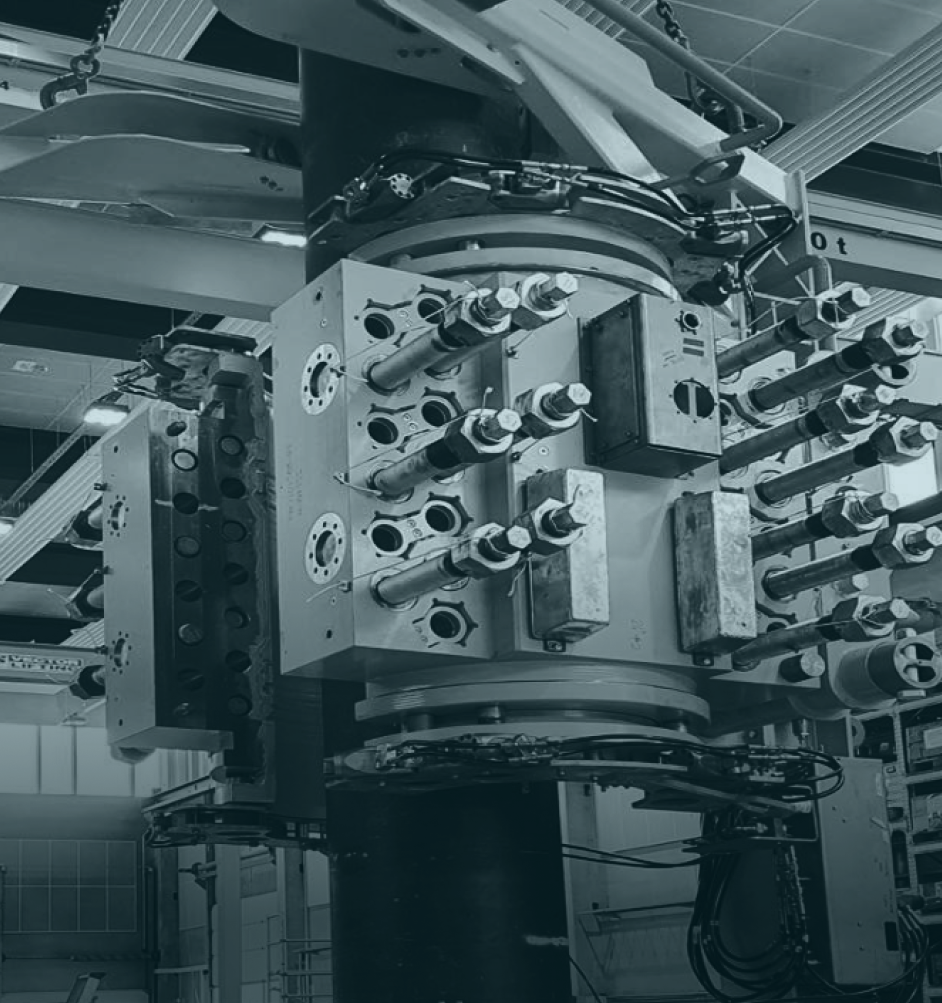
High Pressure PRS for multiple pipe dimensions
India Pipeline High Pressure Deepwater PRS challenges solved by IK Subsea utilizing brilliant engineering across multiple pipeline dimensions.
High Pressure Deepwater PRS challenges solved by IK Subsea despite Covid restrictions, by utilizing brilliant engineering combined with real time remote testing & witnessing
Over the last 10 years, IK-Group’s Subsea business area has regularly delivered repair solutions for deep water fields way beyond the North Sea. Typical locations include West Africa, Brazil and the Far East. The water depths are significant – down to 2000m+ – and the solutions are almost always ROV installed.
So when we were approached by an Indian energy company for a pipeline repair system (PRS) on a deep-water pipeline, we were well within our comfort zone. However, when we finished the initial design brief, we learned that the specification for the repair was on pipelines from 16” to 24” with gas operation and pressure ratings up 433bar. We realized at that point that we’d need to think differently about how we approached this project.
The pipelines were located in a deep-water gas and oil field on the East Coast of India, in the Bay of Bengal. Water depth in the block area ranges from about 400m in the northwest to about 2300m in the southeast.
Guided by our ethos “Challenge Accepted”, IK Subsea bid for and was subsequently awarded the project PRS delivery. The award included an EPRS (emergency pipeline repair system) for reinstating the sealing and structural capacity for possible leakage or damage covering three pipelines: 16”, 18” and 24”. The system was also required to operate from 2000m to the splash zone.
In addition to the challenging job specification, this was all to be successfully executed during the COVID-19 pandemic. This meant each element would need to be undertaken remotely, including live cameras set up in the testing bays, so that the client could witness in real-time as the tests were carried out and approved by the appropriate testing bodies.
IK Subsea has previously designed and delivered equipment for deeper water than the 2000m depth in this project and delivered pressure retaining systems for pressures well above the 433bar specified. However, the combination of large pipeline diameters with thick walls which give significant diameter tolerances, and the high gas pressure introduced an additional challenge.
Upon being awarded this tender, our main focus was on the sealing arrangement, the large tolerances, the high pressure and the gas operation. IK Subsea has developed analysis and design procedures for sealing arrangement on pipelines for repair clamps, plugs and caps. However, the requirements for this system were close to or above the limits of existing designs, requiring a design review and qualification plan for the sealing arrangement.
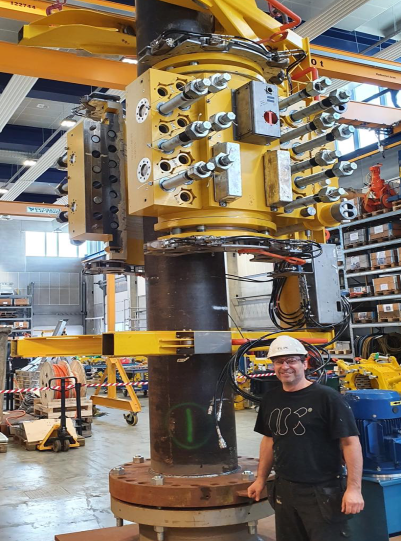
Clamp Design and features
The sealing system comprising a compression packer was designed and tested in a scaled down test rig to ensure a robust system allowing for both the large tolerances of the pipelines, and the high pressure. The lifetime and material properties used were selected and documented based on well understood specifications. The final design of the full-scale repair clamps was based on the analysis of the clamp, the qualification test results and material specifications.
The clamps were designed, manufactured and successfully pressure tested to 650bar.
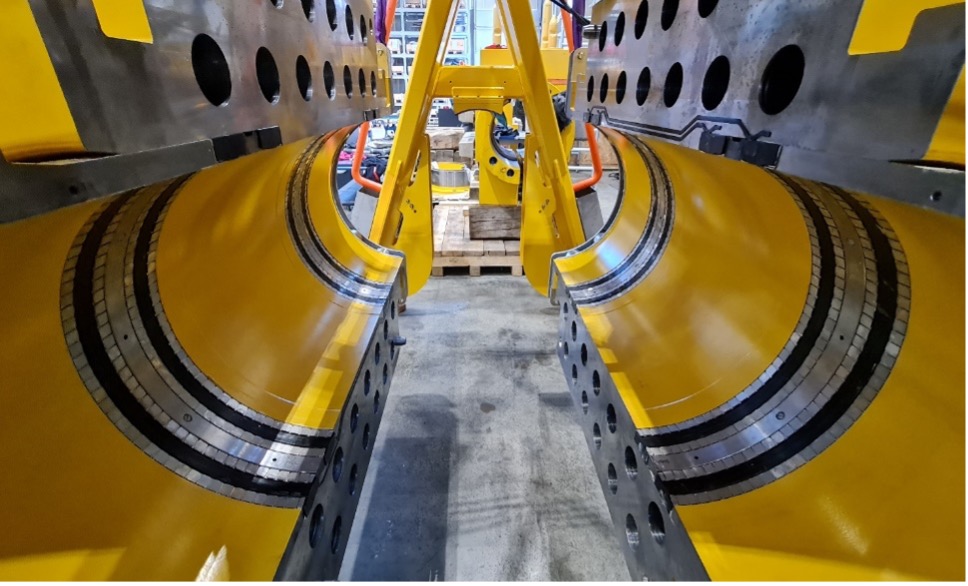
The Clamp Design – Structural Capacity
The repair system’s requirement to reinstate the structural integrity of the pipelines are facilitated by the IK Subsea slips system – qualified for handling the mechanical loads that will be faced at a damage location site.
Due to the large dimensions and the high pressure, the structural components of the system were designed for separate installation, with two separate modules installed on both sides of the sealing clamp in the centre. By utilizing this approach, the installation weights were reduced as were the size and weight of the installation tool.
The system also allows a sealing repair without the need for additional structural support which gives flexibility in terms of multiple repair scenarios.
The installation system
The installation tool is a combined lifting and handling tool, facilitating the installation onto all three pipeline dimensions. The tool can be used for pipe angles from horizontal right through to the vertical risers.
The system is entirely powered and controlled through the ROV hydraulic supply, requiring no surface system or units. The repair clamps are installed and connected onto the pipelines by bolts, set by torque tools at calculated and tested values to give the correct pretension in the bolts. These tools are all recovered to the surface after installation and successful pressure testing through sealing test ports. This leaves the repair system with no hydraulic components or fluids.
Testing, Real Time remote Witnessing and Qualification
Travel restrictions caused by Covid were a global challenge necessitating a different approach to meeting the customer witnessing and acceptance requirements for the Pipeline repair system and Emergency pipeline repair system testing. IK Subsea utilized real time video and communications tools acceptable to the customer engineering teams allowing an interactive approach to a complex testing and qualification program. DNV were physically present in their capacity as an accreditation body, allowing an independent full qualification of the system tests.
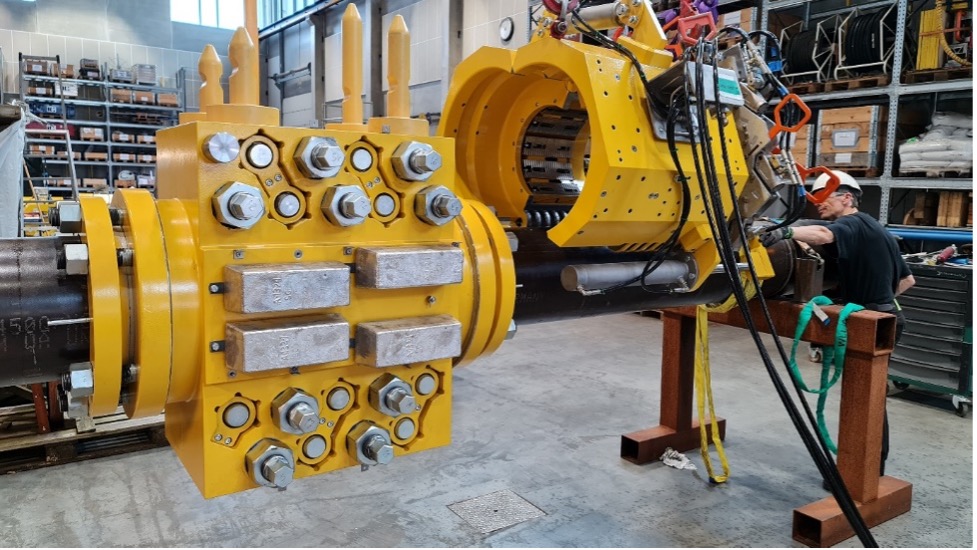
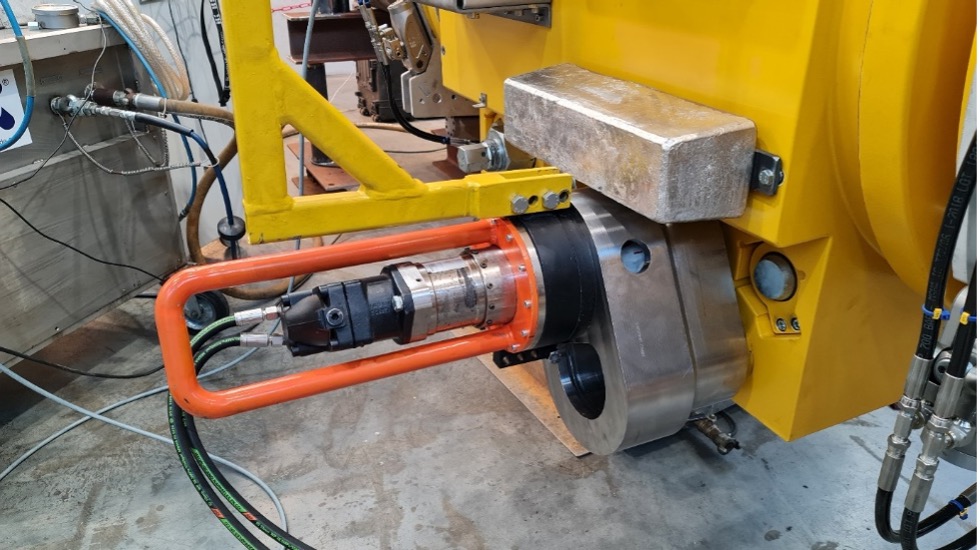
Outcome
The IK Subsea team successfully designed, safely tested, qualified and delivered a Pipeline repair system and Emergency pipeline repair system, capable of operating in Ultra Deep water at high pressure to the client on time and on budget.
The Unique installation tool covered all three pipeline sizes.
Despite the different pipe sizes and tolerances, IK Subsea’s brilliant engineers were able to utilize existing designs in addition to a smart re-design process, minimizing cost and delivery schedules resulting in a win-win for all parties.
The clamp design brings flexibility which allows use across a range of repair scenario’s irrespective of pipeline inclination or orientation.
IK Subsea and the client have laid the groundwork for use of Real-Time witnessing of Factory Acceptance Testing. By establishing equitable and robust processes, both time and cost were reduced without compromising strict customer qualification requirements. The processes established at IK Subsea will allow carbon footprint reductions through minimizing travel wherever appropriate.