This website uses cookies so that we can provide you with the best user experience possible. Cookie information is stored in your browser and performs functions such as recognising you when you return to our website and helping our team to understand which sections of the website you find most interesting and useful.
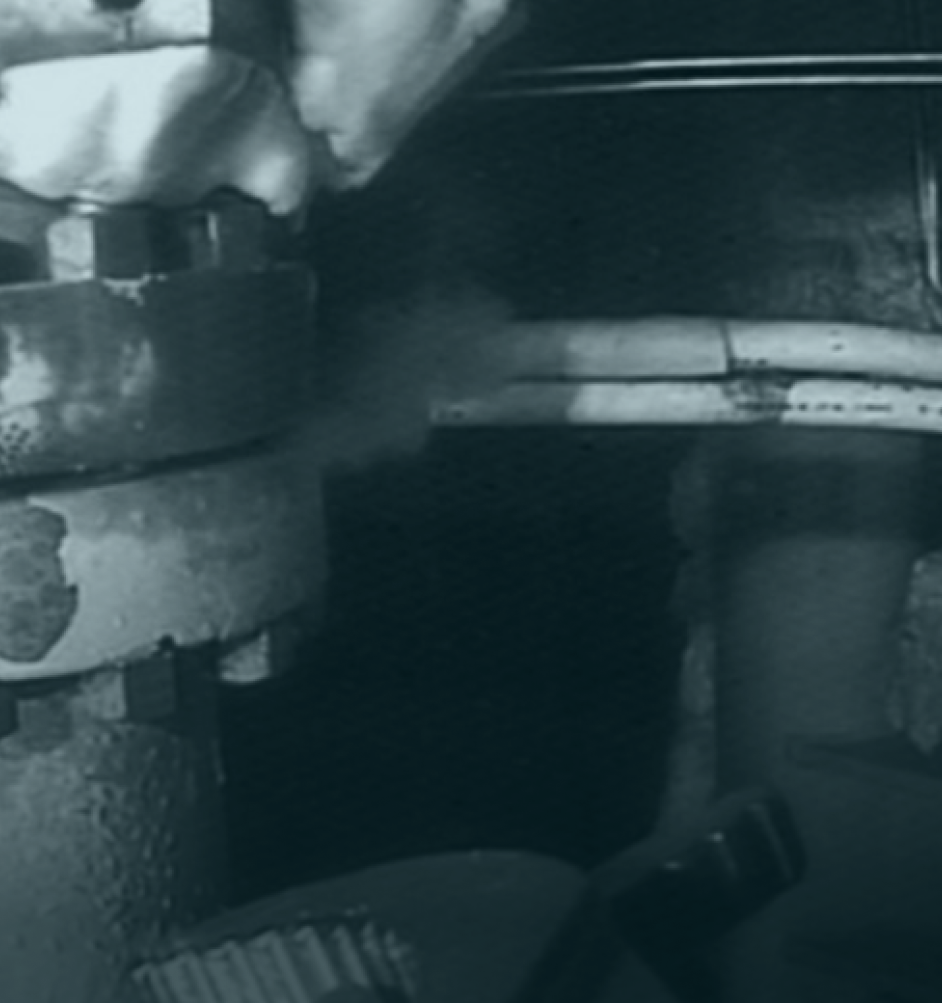
Philippines in-situ Xmas Tree repair
Supermajor recognizes IK Subsea solutions with Outstanding Achievement award for in-situ repair to critical Deepwater gas Xmas Tree by utilizing unique designs.
Supermajor recognizes IK Subsea solutions with Outstanding Achievement award for in-situ repair to critical Deepwater gas infrastructure utilizing unique design
IK Subsea is recognized throughout the energy industry for applying brilliant engineering to complex challenges, with a track record encompassing repair solutions for deep water fields way beyond the North Sea. Typical locations include West Africa, Brazil and the Far East. The water depths are significant – down to 2000m+ – and the solutions are almost always ROV installed.
Shell approached IK Subsea with a challenge where a Xmas tree flange coupling was leaking high-pressure gas at a depth of 820 meters on a producing gas field which is key to the needs of the Philippines market. The Operator had investigated several options, but none were viable, meaning that the tree would need to be pulled for a full workover or replacement unless IK Subsea could come up with a robust and timely solution.
Whilst the high-pressure gas leak was not in itself an insurmountable problem, the leaking flange coupling was difficult to access, with a gap between the upper flange bolts and XT choke body of a mere 37 millimeters making use of existing clamp designs unfeasible.
The IK Subsea engineering team investigated two possible concepts focused on a new flange coupling clamp isolation design and a flange face clamp design with an integral sealant injection system. Both designs were presented to the client at an engineering concept select workshop, where SWOT analysis of both systems was reviewed together with credible design, fabrication, test and installation scenarios.
A unanimous agreement was reached on pursuing the repair clamp design with integrated sealant injection port.
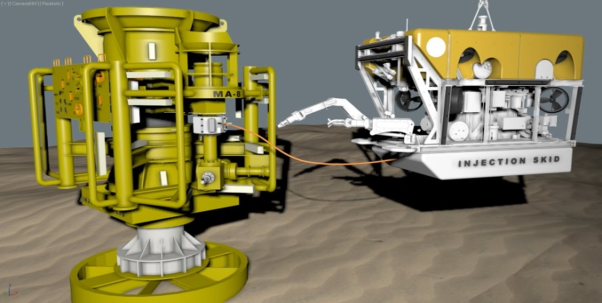
Clamp Design and features
The sealing clamp design was required to satisfy several key attributes which included: effecting a permanent gas tight seal around the flange coupling whilst fitting around existing flange stud-bolts.
Meeting all accessibility requirements, ensuring installation despite a minimal gap above the clamp to XT block of 37 millimeters.
Incorporating a sealant injection port and separate vent in the clamp, meeting sealant flow and viscosity requirements. The sealant is designed to first ensure free flow through all paths, including flange bolts, with the capability of flushing debris through a vent valve, in addition to finally effecting a gas tight seal around failed gaskets or other leaking zones.
A comprehensive testing program was designed to ensure all stakeholders had full confidence in the entire system. The program included elastomer seal tests, leak path testing around the existing and seal clamp bolts, leakage rate tests and sealant injection flow path testing. Furthermore, functional testing included rapid gas decompression, pressure and temperature cycling and life cycle tests and analysis as well as an injection skid test.
To ensure a holistic approach was taken to the testing regime, prototypes were tested on a spare, identical Xmas tree at a supply base in the Philippines.
SIT and FAT tests were witnessed and approved by the client prior to mobilization and deployment.
Clamp Design and features
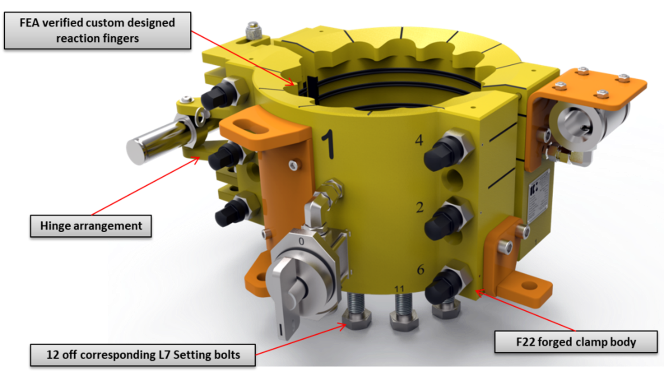
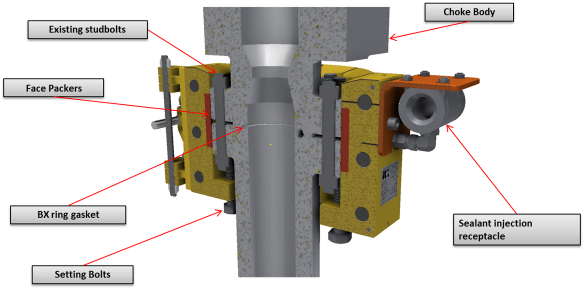
Outcome
The IK Subsea team worked a One-Team approach with the client and contractor as part of a multi-discipline dedicated project team, overseen by a technical review board consisting of IK subsea and Shell staff.
IK Subsea successfully designed a unique high-pressure clamp which was safely tested, qualified, and delivered to the client on time and on budget.
The Unique tool capable of operating in Ultra Deep water at high pressure was successfully deployed and installed by ROV. The Sealmaker sealant was pumped as per plan and together with the clamp ensured a gas tight permanent repair was achieved.
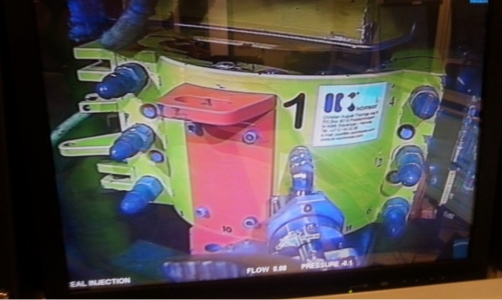
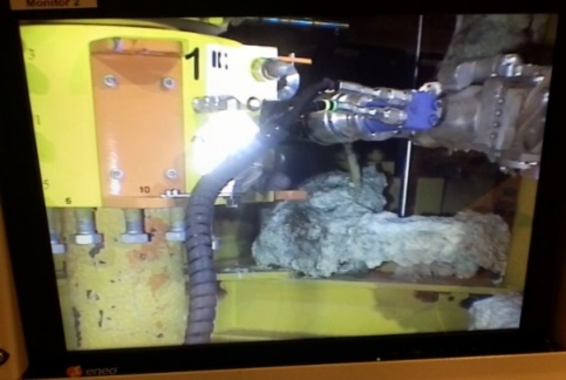
The successful repair avoided retrieval of the Xmas Tree with associated costs and production delays.
Shell Philippines recognized the “Outstanding contribution to the successful repair of the subsea well using a unique design never before attempted” with an Outstanding Achievement Ward to IK Subsea