This website uses cookies so that we can provide you with the best user experience possible. Cookie information is stored in your browser and performs functions such as recognising you when you return to our website and helping our team to understand which sections of the website you find most interesting and useful.
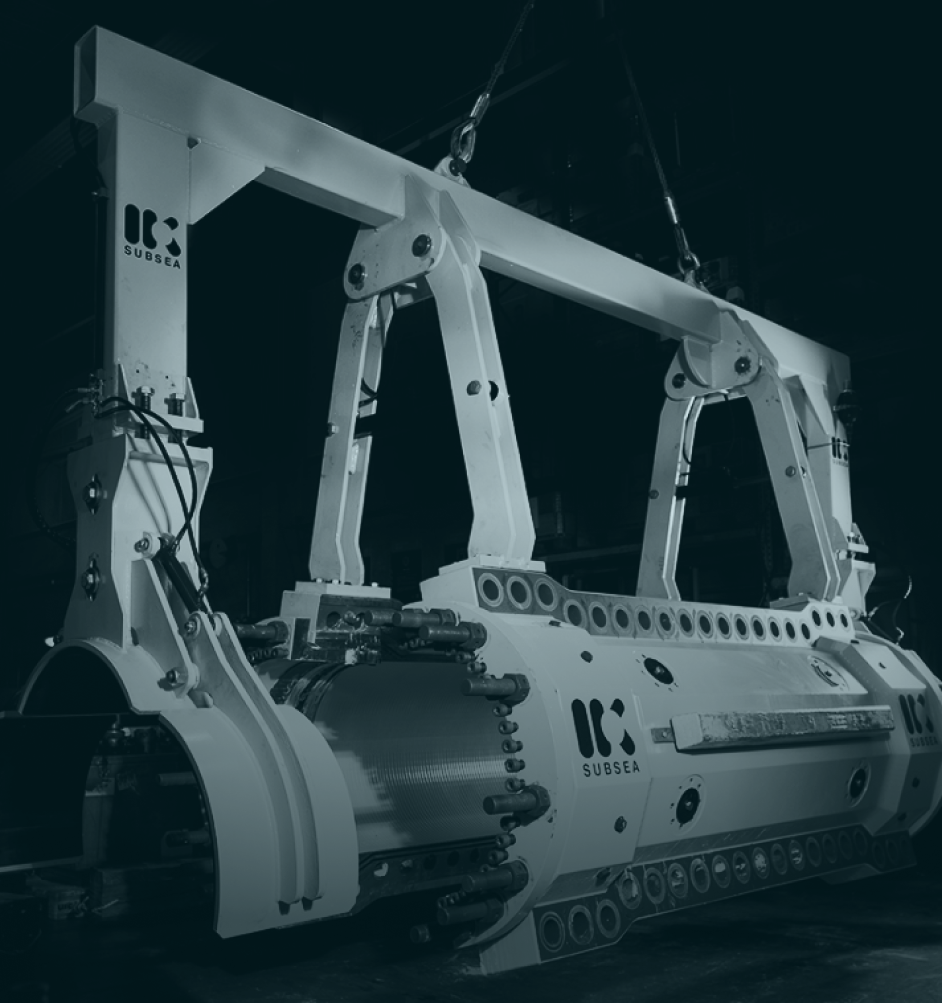
Shell Qatar severe sour service EPRS
Severe Sour Service EPRS requirements solved by unique design and engineering of repair clamps for Middle East pipelines.
Over the last 10 years, IK-Group’s Subsea business area has regularly delivered repair solutions for shallow and deep-water fields way beyond the North Sea. Typical locations include West Africa, Brazil and the Far East.
In the summer of 2021, a Supermajor sent out an industry wide enquiry regarding provision of an EPRS (Emergency Pipeline Repair System) for a high pressure sour service 30” subsea Gas pipeline at 135 bar – capable of meeting exacting requirements.
IK Subsea responded with conceptual designs and were selected to perform detailed design, testing and manufacture of a dual barrier EPRS system complete with lifting and installation tooling.
The IK team worked closely with the client performing design reviews and testing on several iterations of the system, which were primarily focused on primary seals as well as secondary injection of sealant compounds. In special circumstances, customers may be concerned about elastomer performance in extreme sour (H2S) environments due to elastomer properties and possible degradation over time. In this instance, the client has instructed IK Subsea that elastomer seals would not be considered, due to concerns around the potential for swelling and resultant risk of hydrogen induced stress cracking (HISC). Hence IK Subsea focused on the opportunities and challenges utilizing PTFE (Polytetrafluoroethylene) seals.
IK Subsea has developed analysis and design procedures for sealing arrangements on pipelines for repair clamps, plugs and caps. However, the requirements for this system were very different from existing designs, requiring a new sealing concept, testing and qualification plan for the PTFE sealing arrangement.
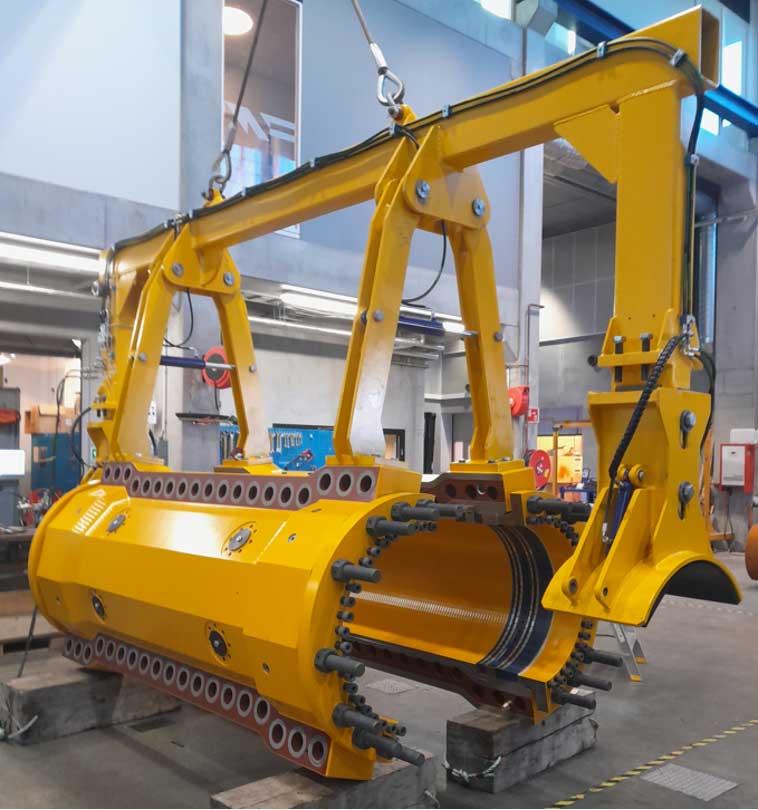
Due to the mechanical properties of PTFE, a secondary barrier was planned, based on previous experience on subsea projects. Sealmaker sealants have been successfully used in challenging environments with IK Subsea clamps and subsea repair tools. Application and design reviews included sealmaker specialists as well as IK Subsea engineers who had previous experience of engineering challenges and solutions to ensure safe and efficient sealant compound injection. Whilst sealant compounds do not typically bond to PTFE, IK Subsea engineering worked closely with our suppliers to review and successfully test acid etching processes which would provide a suitable bonding surface.
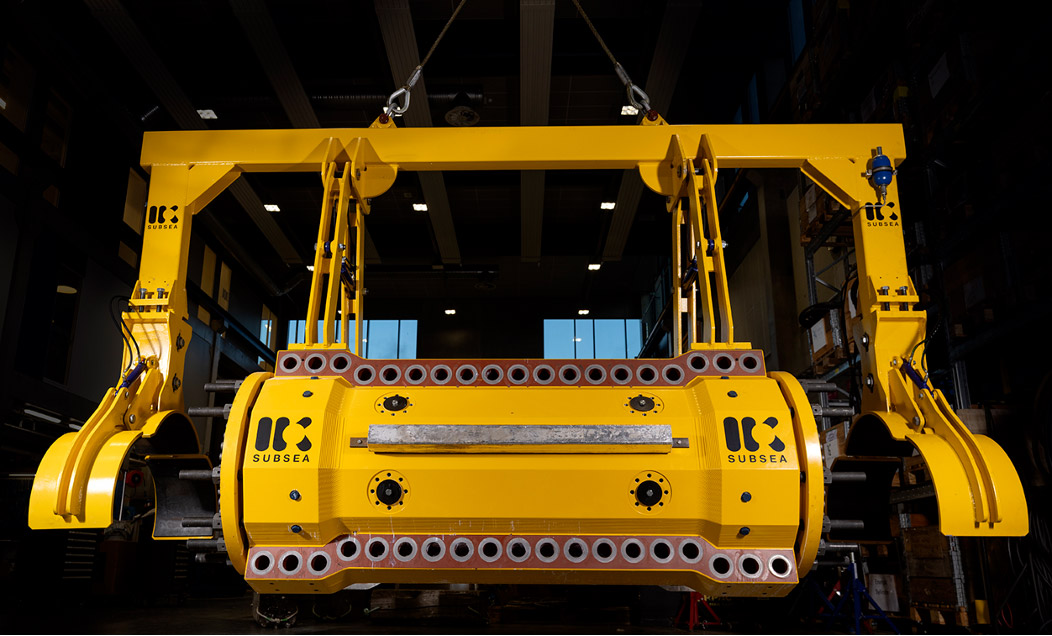
The sealing system comprising several PTFE compression packers was designed and tested in a scaled down phase I of the project was conducted on a scaled down model, phase II was full scale test rig to ensure a robust system allowing for both challenging properties of PTFE, the sour environment, the large diameter of the pipelines, and the high pressure.
The EPRS incorporated a several sealant injection ports and machined channels in the clamp body, designed to ensure free flow for full sealant coverage across the entire surface area including the PTFE seal faces.
The clamps were designed, manufactured and successfully pressure tested to 135bar.
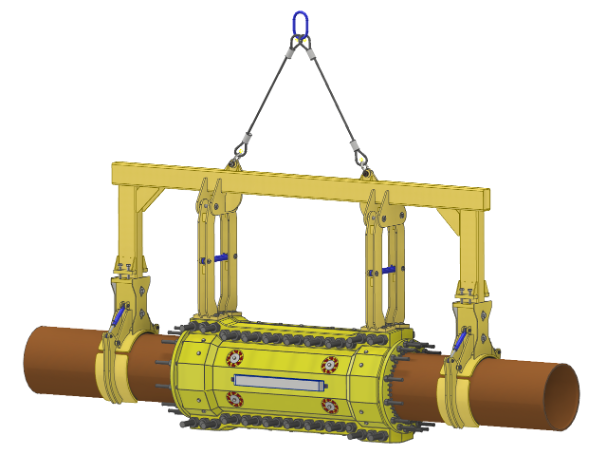
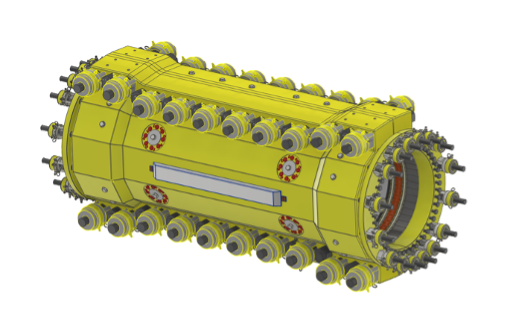
The installation system
The custom-built installation frame is a combined lifting and handling tool, facilitating the safe lifting and installation with diver assistance onto the large diameter pipeline.
The system is hydraulically operated by divers (both the alignment tool and EPRS clamp). The repair clamps are installed and connected onto the pipelines by bolts, set by torque tools at calculated and tested values to give the correct pretension in the bolts. These tools are all recovered to the surface after installation.
Testing, Real Time remote Witnessing and Qualification
A comprehensive testing program was designed to ensure all stakeholders had full confidence in the entire system. The program included PTFE seal tests, leak path testing around the seal clamp bolts, leakage rate tests and sealant injection flow path testing.
Outcome
The IK Subsea team successfully designed, safely tested, qualified, and delivered an Emergency Pipeline Repair System with unique PTFE sealing mechanisms, capable of operating in a high-pressure sour gas environment on budget.
Dual seal designed and tested in addition to Sealent injection barrier.
The custom-built installation tool enables safe and efficient diver assisted installation.
In conjunction with the Client and Sealmaker, the IK Subsea team have delivered an innovative design allowing sealant injection and a secondary barrier.
Despite the unique requirements for seal material selection, IK Subsea’s brilliant engineers were able to utilize existing designs in addition to a smart re-design process, minimizing cost and delivery schedules meeting strict customer design and qualification requirements.
IK Subsea were awarded recognition by the Research Council of Norway.
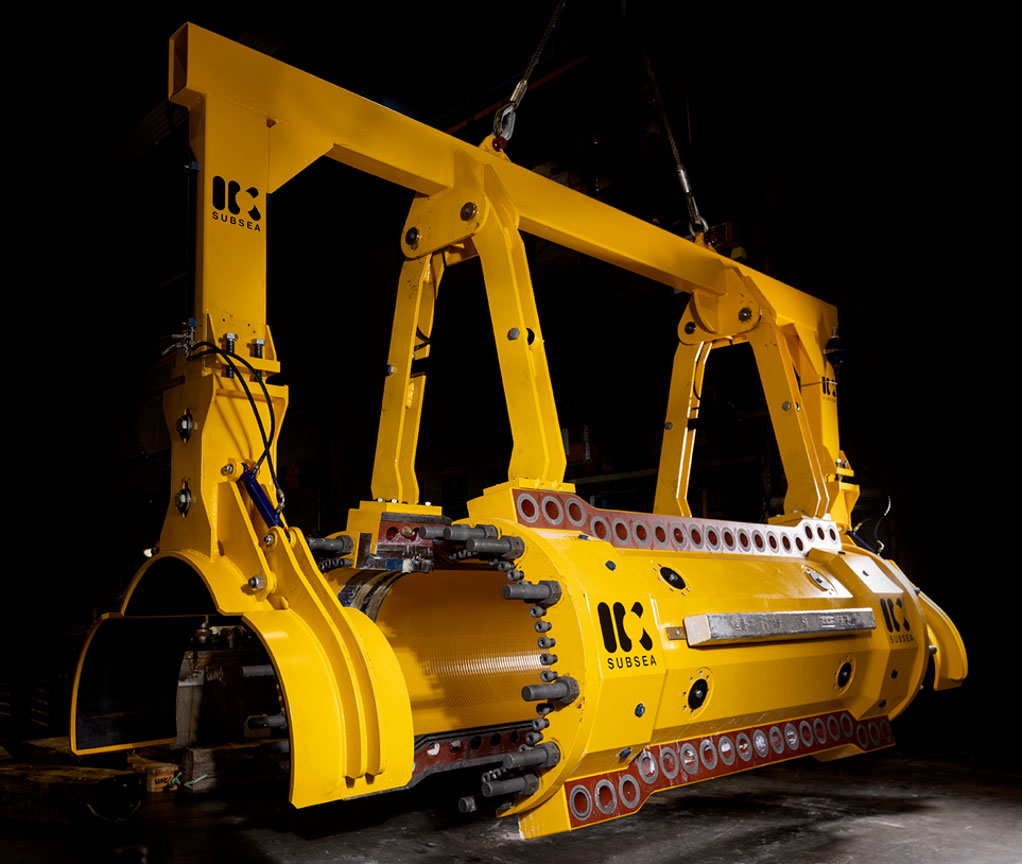
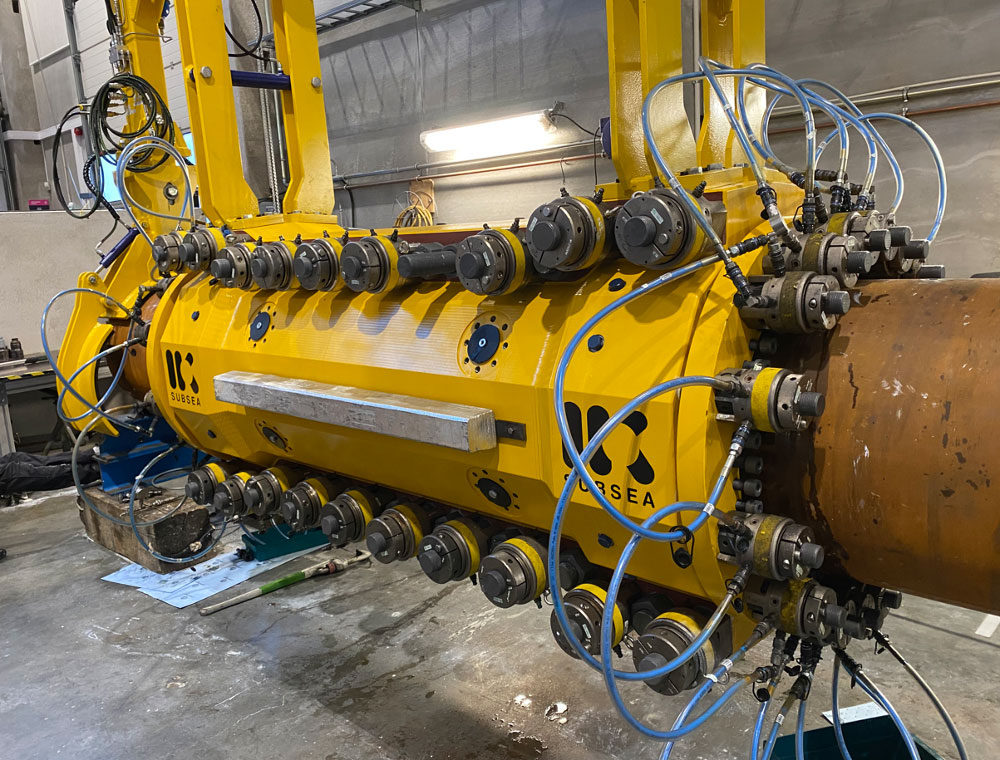