This website uses cookies so that we can provide you with the best user experience possible. Cookie information is stored in your browser and performs functions such as recognising you when you return to our website and helping our team to understand which sections of the website you find most interesting and useful.
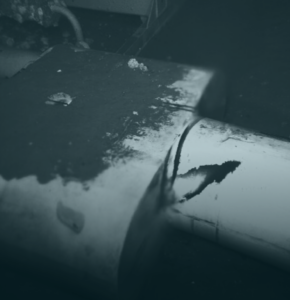
Structural Repair at PLEM Junction – Ultra Deepwater
Unique Engineering and new technology solves leaks and structural failure at PLEM Pipeline junction in Ultra deep water West Africa.
When a Supermajor approached IK Subsea with an urgent problem, our team of brilliant engineers set to work on designing a unique solution which could be delivered quickly. IK Subsea has a track record of repairing pipelines and subsea infrastructure in deep and ultra deep water, but some challenges can truly be described as unique.
The client described the problem in detail. A pressure drop had been observed leading to further investigation, which uncovered a 180° circumferential crack in a 12 inch production pipeline to PLEM junction (pipeline end manifold). The crack location was in the immediate vicinity of the PLEM junction face, with the pipeline under axial loads which exacerbated the problem and hindered a repair solution. The extensive crack in this physical location and environment would normally be beyond the repair capabilities of traditional technologies.
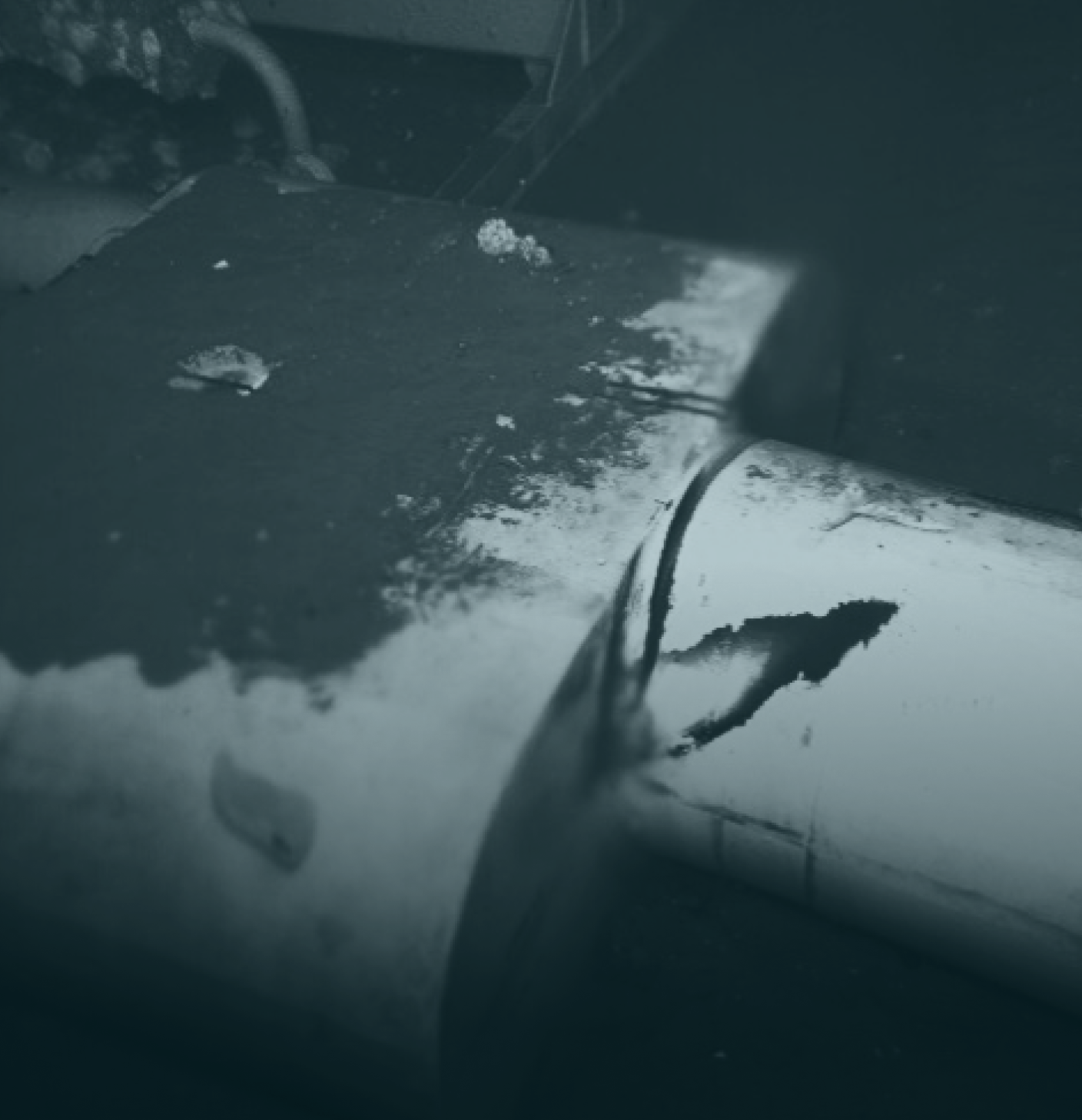
The damaged infrastructure was part of a subsea Oil & Gas producing field offshore Angola, at a water depth of approximately 1500 meters.
The client investigated several solutions, but IK Subsea proposed the only solution which would allow pigging after the repair. Due to environmental concerns, the leak led to a shutdown in production with the associated financial implications. A temporary and/or permanent solution was needed urgently. With Covid restrictions in place across the globe, exceptional focus and attention to detail and fully compliant solutions would need to be applied by IK Subsea and the customer.
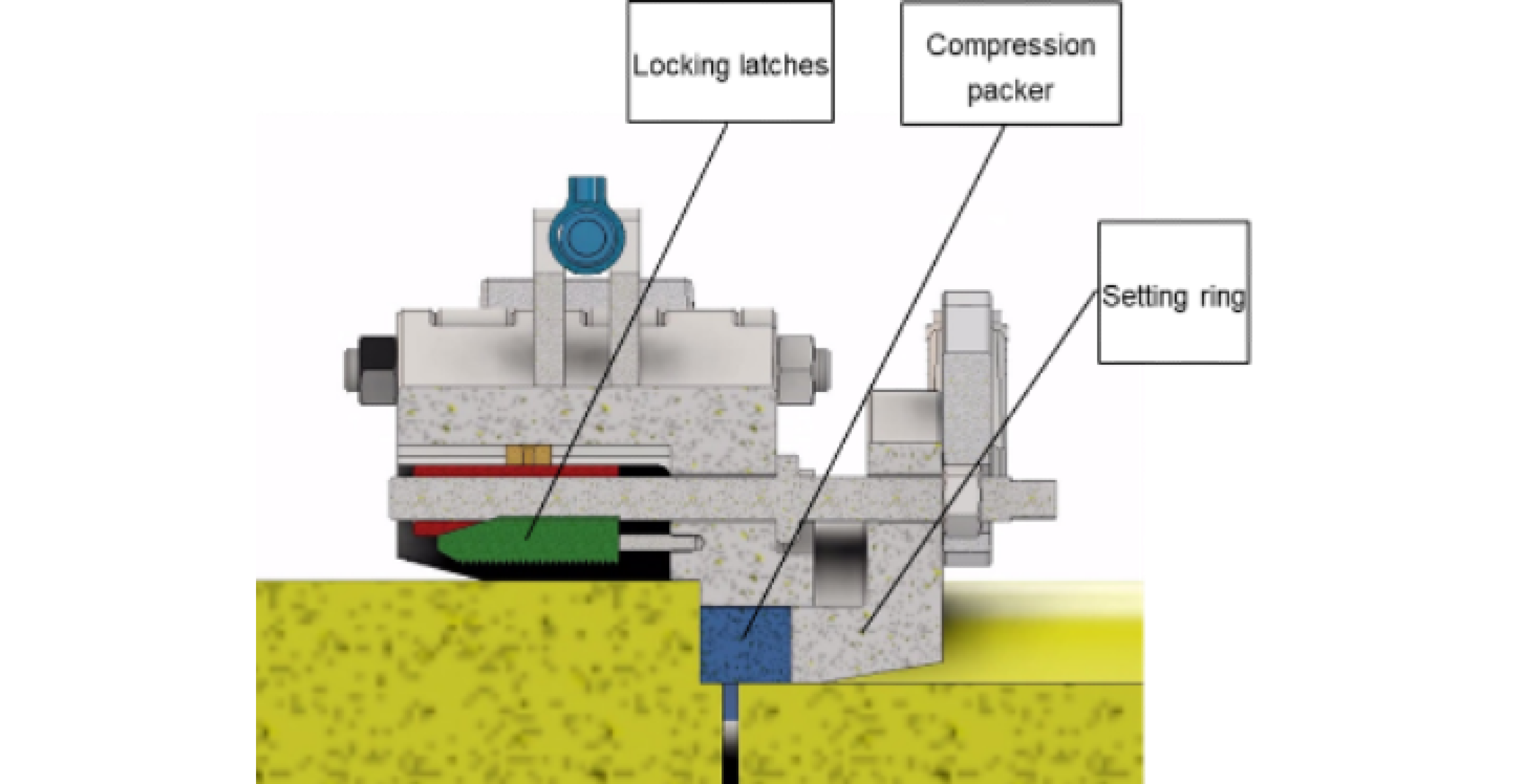
The IK Subsea design team instigated an approach which would relieve stress on the pipeline which was laying at an inclination of around 3° caused by the crack with concerns that the crack would develop, and the pipeline would break apart. In parallel the temporary repair would attempt to seal the leak – although the client and IK Subsea acknowledged that a seal would be unlikely due to the GPSU (glass syntactic polyurethane) coating in place around the visibly large leaking crack. Hydrate formation was a concern, so the temporary seal would also hinder hydrates by minimizing or mitigating water ingress.
The temporary sealing device comprised a patch clamp with seal design and pressures designed to allow a flexible seal at 15 MPa water pressures observed at the depth of the infrastructure. The sealing packer tests covered two different packer hardness’s allowing selection of the best seal with a packer pressure of 90 bar.
Structural reinforcement was addressed by design and manufacture of a structural support clamp which would alleviate the axial loads on the pipe in the area of the crack, hence avoiding further tension loads and damage. The design incorporated a landing platform for the equipment which would be used to execute the permanent repair; saving both time and cost during the critical permanent repair phase
The temporary sealing clamp and structural support clamps were manufactured, fully tested and shipped within 10 weeks. Installation was successfully carried out by ROV, but the leak was not 100% sealed, as a new leak path was detected due to delamination of GSPU coating and steel base pipe. The temporary structural clamp performed exactly as designed providing structural support and stopping further structural degradation.
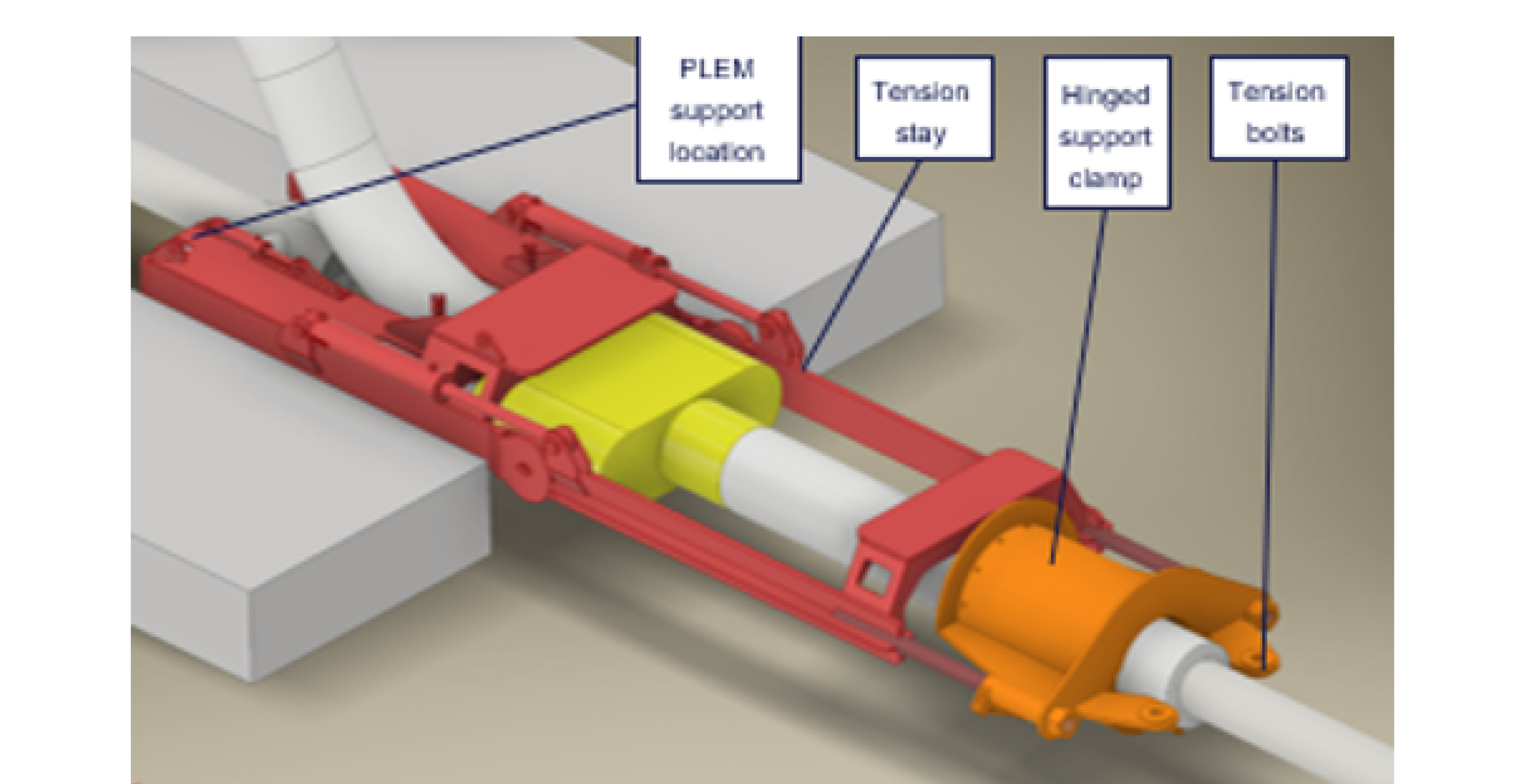
The tool suite for permanent repair of the leak and pipeline integrity was designed and manufactured in parallel with the temporary solution. The structural sealing clamp design and installation needed to overcome several challenges, including space limitations and access to clamp setting bolts in addition to the sheer size of the crack and high pressures and loads. The compact Integrity clamp design ensured that a full seal would be achieved around the elastomer compression packers, with a slip design incorporating a wedge and setting ring to ensure a robust physical loading of the packers via the slips. An IK Subsea patented design allows the clamp bolts to be torqued from one side only, which was critical to overcoming the access limitations.
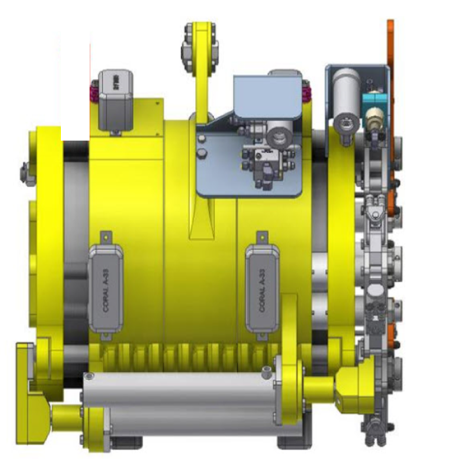
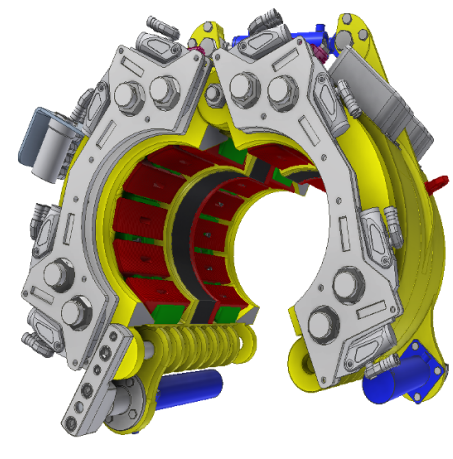
The installation system
In addition to the permanent structural clamp and compact integrity clamp, a subsea ROV operated tool suite was manufactured to fit the required interfaces including the landing plate which had been designed into the temporary repair solution. The tool suite ensured efficient coating removal around the sealing clamp location as well as removal of the cracked weld and stiffener plate.
The system is entirely powered and controlled through the ROV hydraulic supply, requiring no surface system or units. The repair clamps are installed and connected onto the pipelines by bolts, set by torque tools at calculated and tested values to give the correct tension. These tools are all recovered to the surface after installation and successful pressure testing through sealing test ports. This leaves the repair system with no hydraulic components or fluids.
Full Factory acceptance and system integrity tests were carried out at IK Subsea workshops as well as wet tested at Oceaneering facilities in Norway, whilst ensuring full compliance with all Covid restrictions.
Testing, Real Time remote Witnessing and Qualification
Travel restrictions caused by Covid were a global challenge necessitating a different approach to meeting the customer witnessing and acceptance. IK Subsea also utilized real time video and communications tools acceptable to the customer engineering teams allowing an interactive approach to a complex testing and qualification program.
Outcome
The IK Subsea team successfully designed, safely tested, qualified and delivered temporary and permanent repair solutions in an expedited short timeframe.
The Unique design incorporated all the interfaces, including a landing frame, in the temporary repair solution, saving time and cost during the GPSU coating removal process and the permanent repair.
IK Subsea’s brilliant engineers were able to utilize existing designs where appropriate, minimizing the need for a totally new approach – despite the unique challenges of the structural pipeline failure and leak.
The temporary repair stopped further structural degradation of the pipeline.
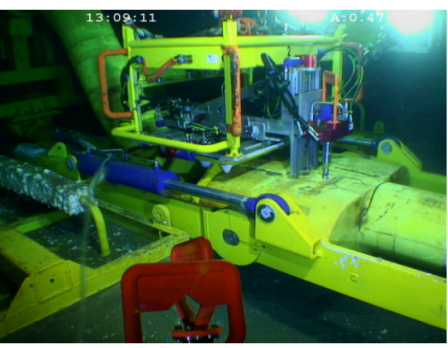
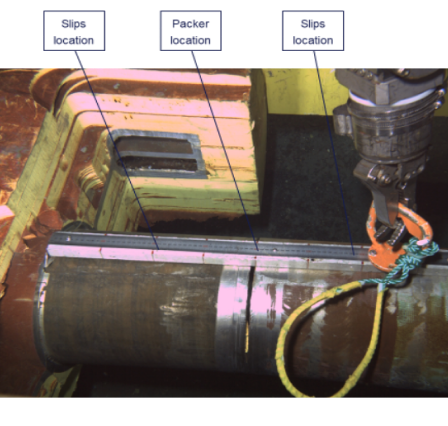
Despite the complexity of the repairs and the limited access at the crack location, the repair and installation process was undertaken as planned without HSE incidents.
The permanent repair was pressure tested and proven after an operation that required millimeter precision milling and removal of GSPU, steel structural anchor supports and load transfer plates as well as corrosion and welds. The subsequent installation of the IK Compact Integrity clamp and structural repair clamp performed as designed, taking the loads previously taken by fillet weld connections and a soil anchor, allowing full production reinstatement. The permanent repair has been designed for a 25-year lifetime. An additional benefit of the IK Subsea solution is that pigging operations can resume as and when required.