This website uses cookies so that we can provide you with the best user experience possible. Cookie information is stored in your browser and performs functions such as recognising you when you return to our website and helping our team to understand which sections of the website you find most interesting and useful.
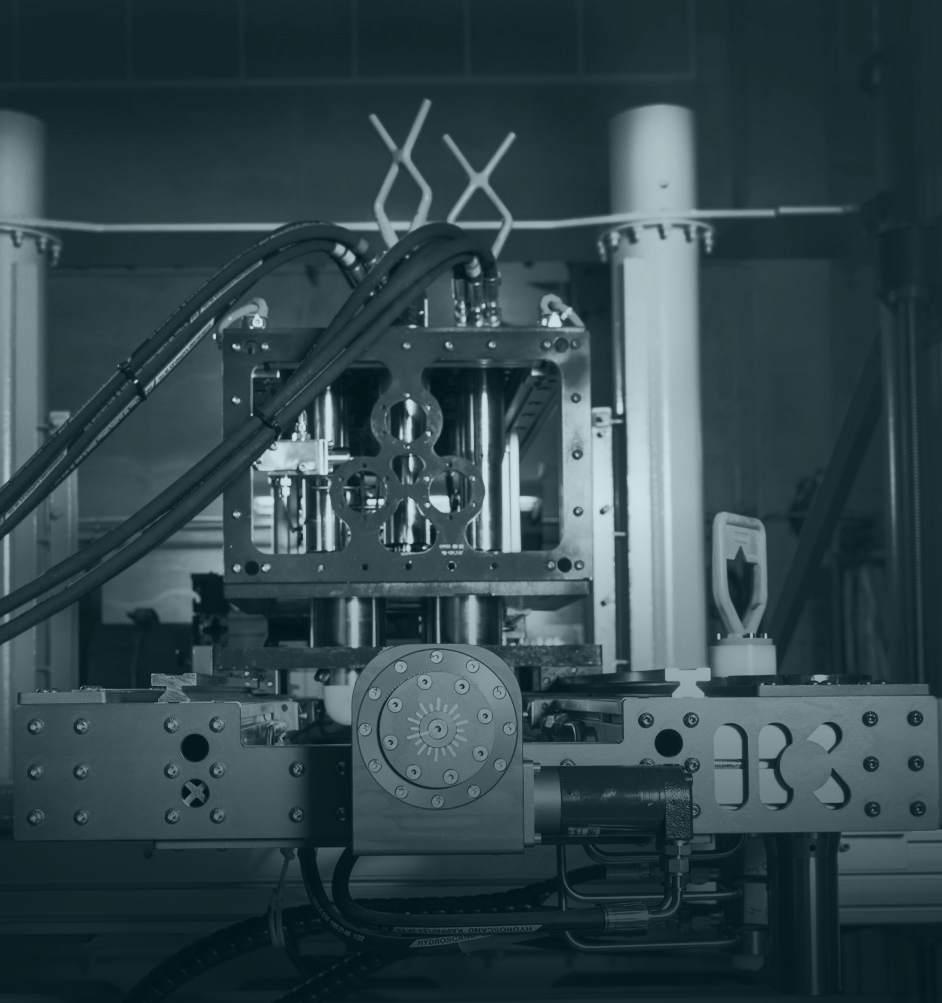
Xmas Tree Flange Repair – Ultra Deepwater
Design, Testing and Utilization of unique subsea tool suite allowing in-situ repair of leaking flanges on Deepwater Xmas Trees in West Africa
Design, Testing and Utilization of unique subsea tool suite allowing in-situ repair of leaking flanges on Deepwater Xmas Trees
IK-Subsea was contacted by a Supermajor with an inquiry related to an external leakage detected in 2019 on a water injection Christmas Tree.
The Xmas tree was recovered in February 2021 and multiple issues were observed including failed connections.
The failures were of additional concern as other subsea infrastructure in the field exhibited similar leakages.
IK Subsea performed a study to explore, evaluate and establish a process and equipment required for in-situ repair of the leakages. As both space and access were limited, in-situ repair was regarded as challenging and complicated. However, the benefits of sub-sea in-situ repair were considered substantial, based on avoiding mobilization of vessels to retrieve the trees, costs (and time) of repair, plus re-installation with the subsequent costs and risk. The client invited IK Subsea to perform a study with the following focus areas:
IK Subsea performed a study to explore, evaluate and establish a process and equipment required for in-situ repair of the leakages. As both space and access were limited, in-situ repair was regarded as challenging and complicated. However, the benefits of sub-sea in-situ repair were considered substantial, based on avoiding mobilization of vessels to retrieve the trees, costs (and time) of repair, plus re-installation with the subsequent costs and risk. The client invited IK Subsea to perform a study with the following focus areas:
The possible solutions – early evaluation
The IK Subsea team worked and reviewed several solutions, narrowing in to two primary possibilities focused around either the Diverter Block Blind Flange / blind location and the IWV Block Flange / the flange location. Technical and cost constraints of possible repair solutions led to the flange location being eliminated from the study.
Three possible solutions were found to be realistic and viable for the blind location:
- Replace the existing flange bolts and nuts.
- A brace solution giving sufficient support to the existing blind and replacing the structural capacity of the blind flange bolts.
- A plug solution by removing the blind flange and replace it with sealing the 5” drilled hole in the block.
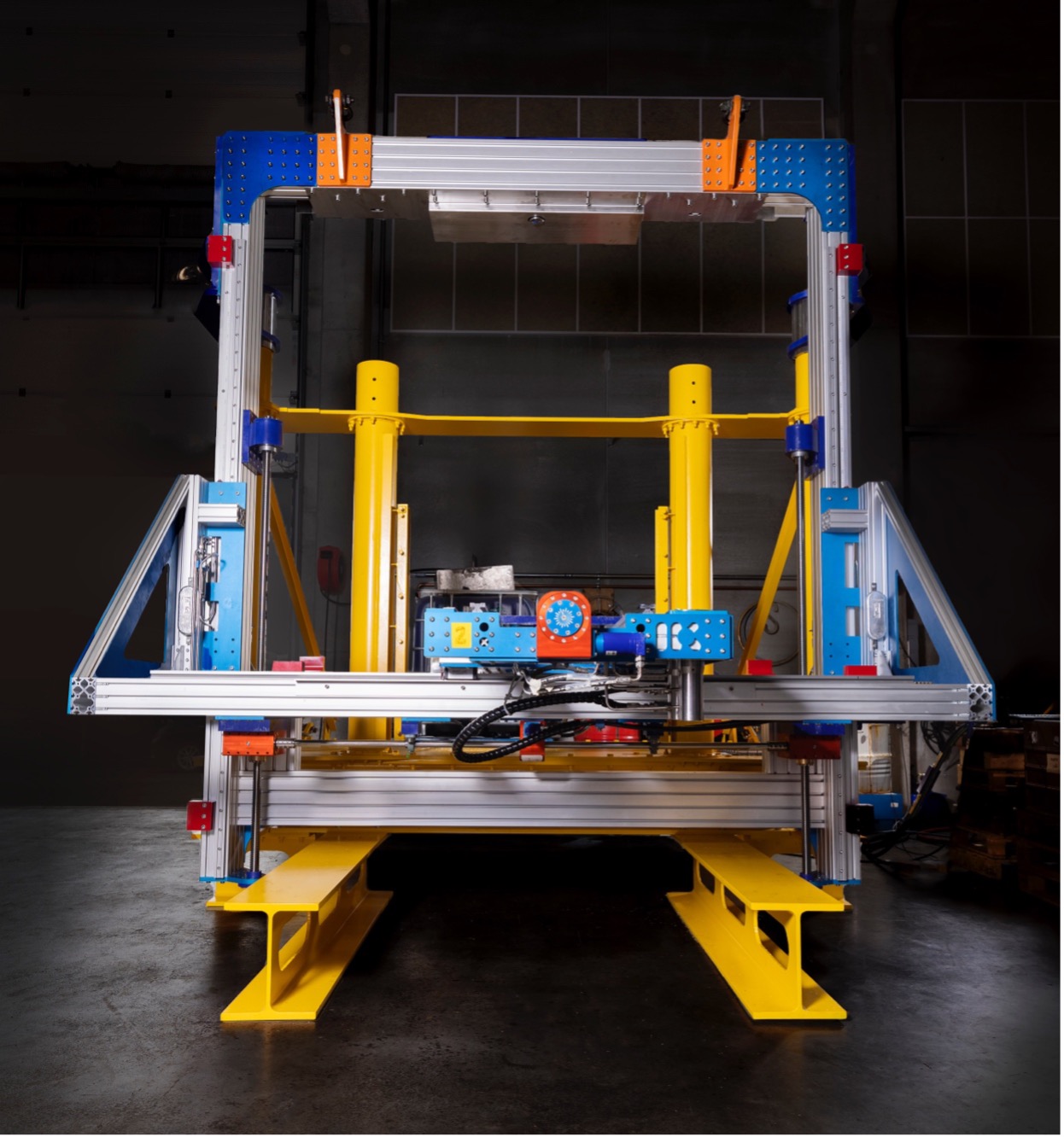
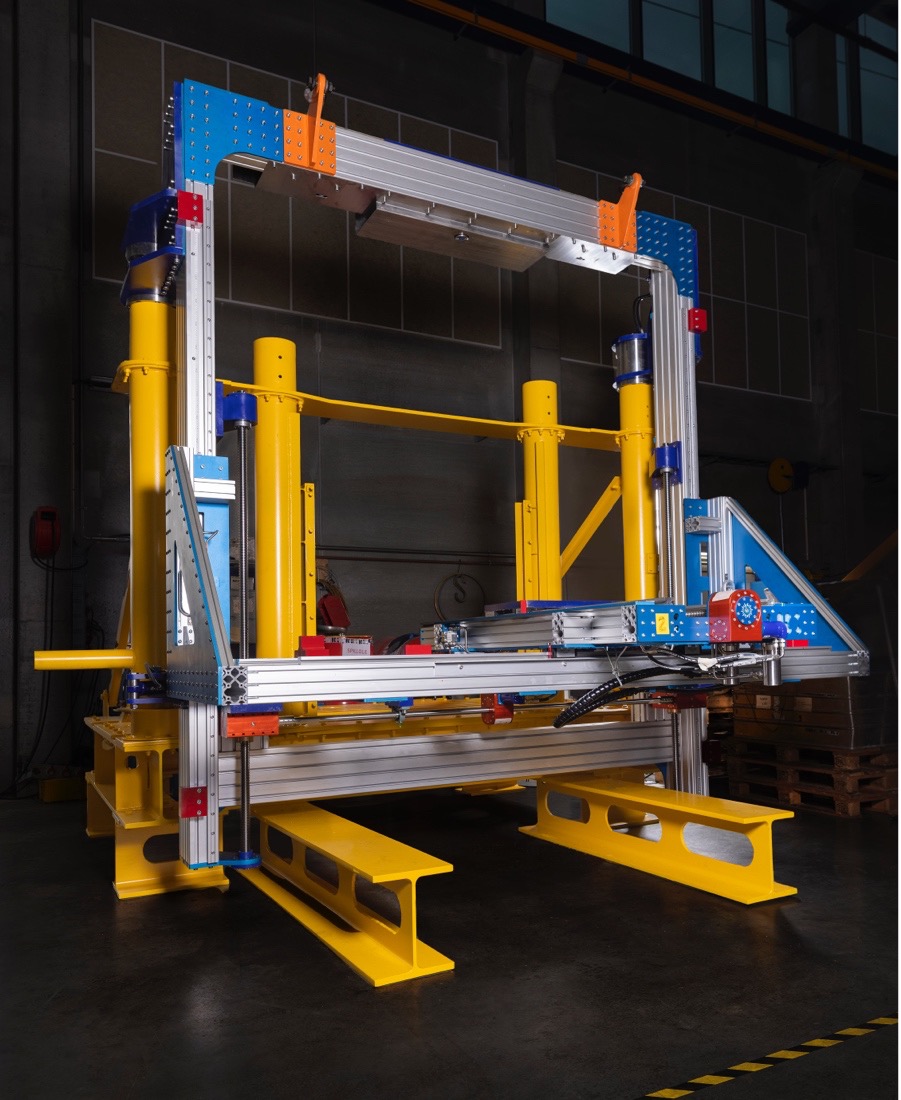
From solution concept to primary candidate
Selection of the preferred solution was based on integrity focused risk evaluations and separate reviews of the required installation operations for each concept. The engineering team at IK Subsea evaluated replacing the existing flange bolts and nuts which was scored as a solution with high integrity, but the installation operation was considered to have a low probability of success. The team also analysed an additional brace solution, using either four or two support braces. Whilst both solutions were regarded as feasible, upon evaluating the integrity of a repair method after several of the existing flange bolts had broken, it was concluded that this was not a viable solution. The sealing integrity was also considered a challenge. This solution was finally considered as a possible preventive solution for locations where no damage was apparent, to prevent future bolt failures. Thirdly, the Team evaluated a plug solution. The plug solution was considered a high potential solution, but several issues would need to be addressed and closed out in the detail design and testing/qualification phase of the project.
Operational qualification and testing
The main running frame and all the 14 different tools were extensively tested in the IK Subsea workshop.
The extensive test program was successfully completed. One of the key components was the wire cutting tool which proved to be challenging, but after design modifications this key component proved to be reliable and ready for deployment.
After successful workshop tests, the same program was performed wet in a test pit remotely operated by ROV. The client was intimately involved throughout the testing and qualification process allowing a high degree of confidence prior to deployment to the deepwater offshore location.
The offshore operation
The offshore operation was executed in the spring of 2023 over a period of 2 weeks. The vessel and ROV contractor utilized personnel and learnings from the testing and qualification process, ensuring smooth on-site execution at approximately 2016 meters water depth.
The equipment package was mobilized from Norway, together with an experienced crew from IK Subsea to ensure a flawless operation. The campaign consisted of permanent repairs to leaking flanges on two Xmas trees which were key components in the water injection subsea infrastructure on the field.
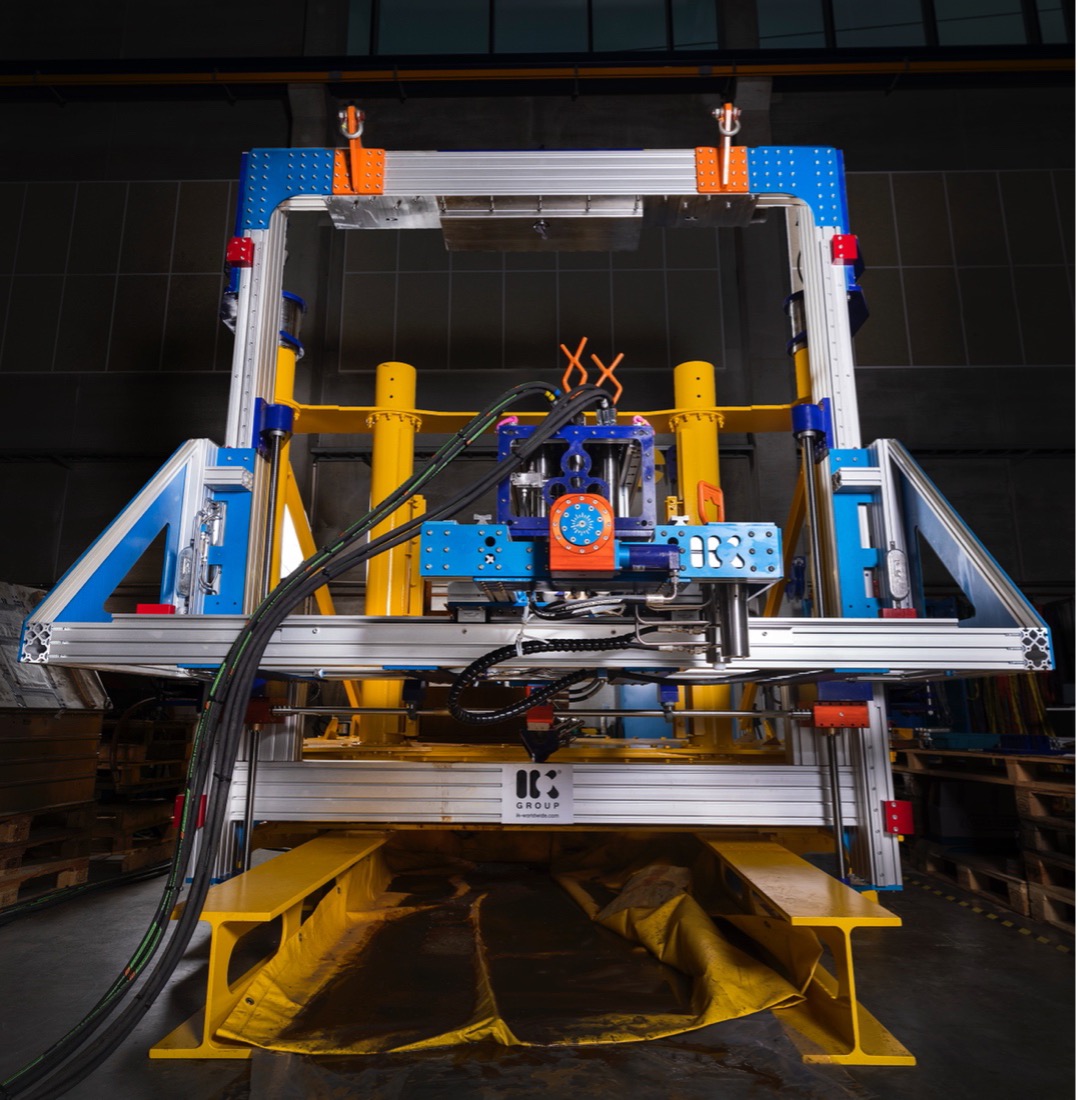
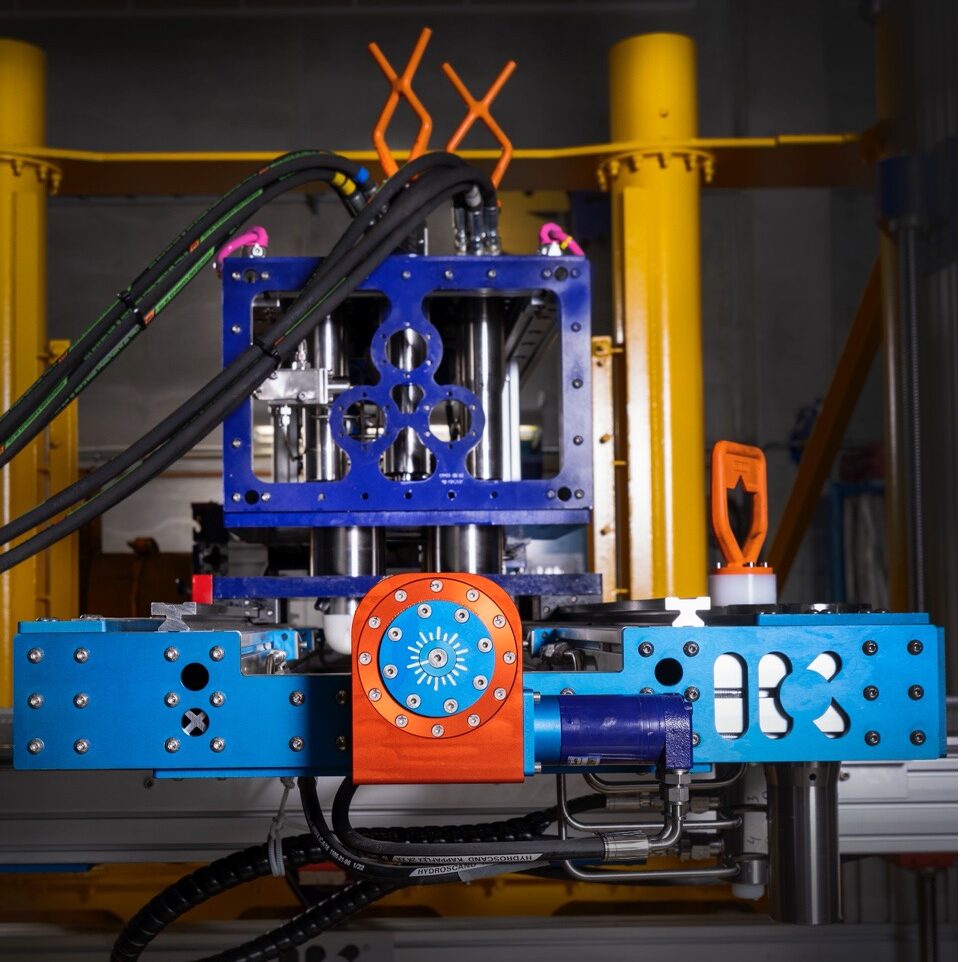
Outcome
The leaking flanges were successfully plugged and tested on both Xmas Trees. This was a spotlight project for this supermajor, with several first-time achievements:
The first time that in-situ repair had been achieved in such a complex environment.
The first-time use of specifically designed, tested and manufactured equipment of this type.
This project saved the client significant costs. The only available alternative to the IK Subsea solution was to pull the Xmas trees with the corresponding operational cost, tree refurbishment cost and time, plus the re-installation cost and time – all with significant reductions in production.
The IK Subsea team was focused on safety and flawless execution throughout the operation and delivered an incident free project
The bespoke tool package was designed, manufactured, tested and performed the work on time and on budget.
The tool package and the operation performed as planned and proved to be safe and reliable.
The methodology and tools applied were specifically made for replacing the blind flange with a plug, but the tooling package may be used for other retrofit in-situ subsea repair operations on Xmas trees, eliminating the need for pulling the trees.